Top 10 Frequently Asked Questions About the Mechanical, Electrical and Plumbing (MEP) Team
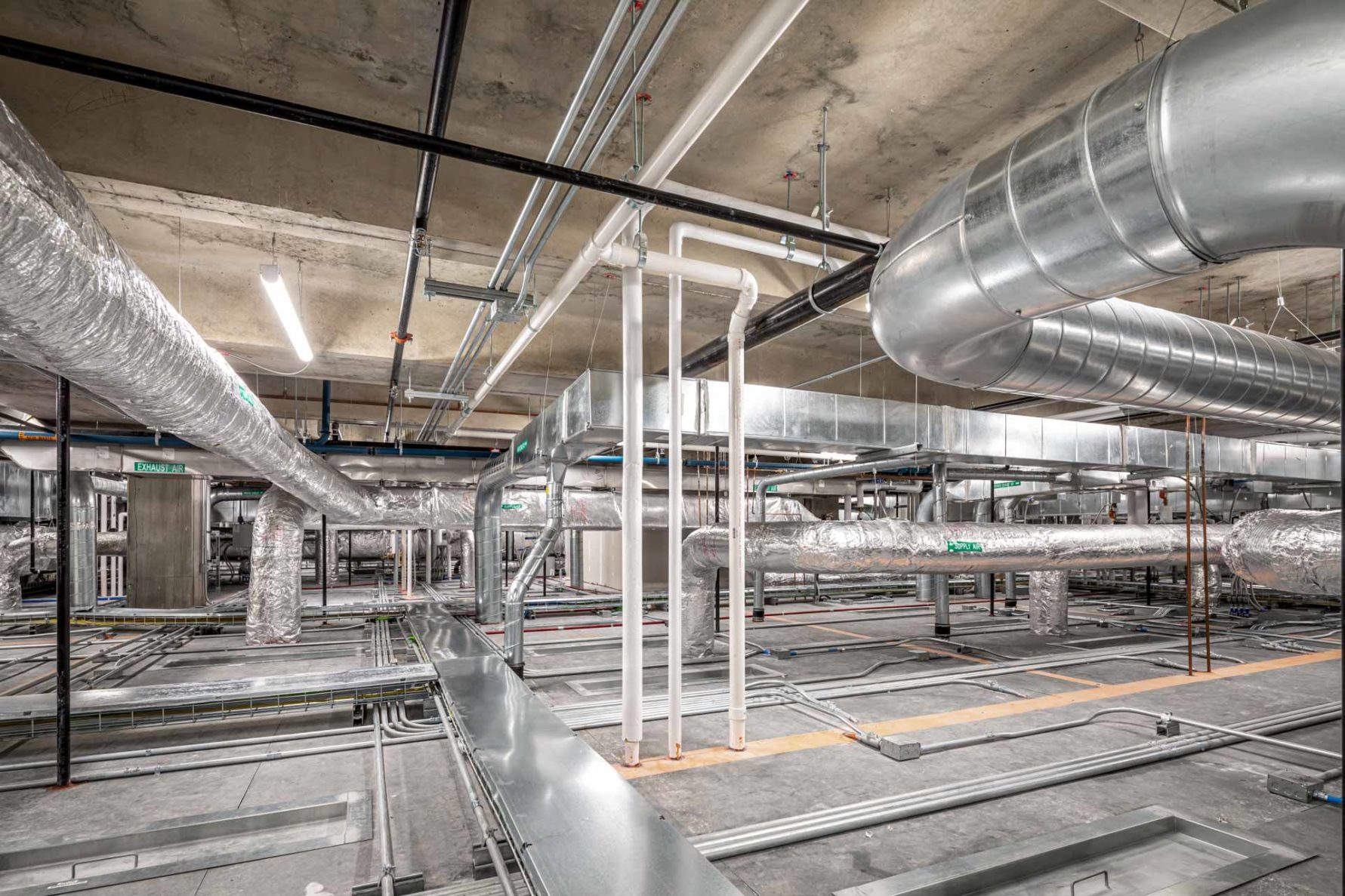
1. Does your MEP team provide engineering design?
We don’t design your project, but many of us used to be designers. Our team includes former design engineers, trade partners and equipment specialists, giving us a deep understanding of how mechanical, electrical and plumbing (MEP) systems come together. We understand what goes into engineering these systems and how they translate to construction. Our role is to bridge that gap—helping owners, design teams and trade partners align on cost, schedule and constructability.
2. How does the MEP team stay involved throughout the project?
The MEP team is engaged from concept through closeout. During preconstruction, we work alongside our estimating team to validate budgets and analyze cost options before they’re presented to the owner and design team. In construction, we observe installations, create non-compliance reports and help resolve field issues. We stay involved through commissioning and turnover to help make sure the final product performs as intended.
3. How do you support value management efforts?
Value management isn’t just about cutting costs—it’s about asking, “Can we do this instead? Is this the best way forward for this project?”. We evaluate design alternatives with a focus on constructability, budget and long-term operations. By bringing in real-world cost and schedule data, we help teams make informed decisions that balance first costs with long-term value.
4. How does your team fit into the preconstruction phase?
The MEP team’s involvement shifts depending on the project’s needs, but we’re always engaged. Whether we’re supporting early procurement, budget accuracy, or cost options, we work closely with our estimating team to ensure MEP budgets are realistic and align with the owner’s goals. Since we sit alongside our estimators, we’re regularly reviewing project budgets and validating numbers before they’re presented to the owner and design team.
5. What do you look for in constructability reviews?
Our goal is to ensure MEP systems are not only designed well but are also constructable, maintainable and aligned with project goals. In early design phases, we help owners and design teams identify potential construction challenges, assess feasibility and explore value-driven alternatives. As design progresses, we focus on factors like system serviceability, installation sequencing and long-term maintenance access—so the systems work as intended from day one and for years to come.
We also identify scope gaps—things that might not be fully defined but have a big impact on cost and operations. HVAC controls, for example, can drive both the project budget and long-term energy costs. By asking questions early, we help clarify design intent and keep budgets in check.
6. How do you manage long lead MEP equipment?
Gone are the days of major equipment sitting on a shelf, ready for immediate delivery—most equipment is now made to order for each project. That’s why we start looking at long lead items as soon as the project concept takes shape—well before the design is complete. We work with estimators, trade partners and vendors to track lead times and develop procurement strategies that align with the schedule. In many cases, we’ll bid equipment directly to vendors before bringing on trade partners, ensuring critical components arrive when needed.
7. How do you support life-cycle cost decisions?
Choosing an HVAC system isn’t just about what it costs today—it’s about what it costs over its entire life. Utility costs often make up 70% of a building’s operational expenses, so these decisions go beyond first costs. We provide Life-Cycle Cost Analyses (LCCA) to compare different system options, weighing initial costs against long-term maintenance and operational expenses. While full energy modeling is typically handled by the design team, we provide the real-world cost data they need to guide the analysis.
8. How do you support construction in the field?
Once the walls close up and the ceilings go in, most of the MEP work is out of sight—but we help make sure it’s right before that happens. The MEP team is on-site, working with project teams, trade partners and vendors to verify rough-in installations, assist with logistics and sequencing, and help navigate coordination challenges. We also bring our system expertise to review change orders, ensuring accuracy and scope so the owner knows exactly what they’re paying for.
9. Is the MEP team on-site full-time during construction?
Our MEP managers aren’t full-time on-site, but we’re highly engaged with our field teams. We make regular site visits, assist with system-specific planning, and support our superintendents and trade partners in implementing the MEP scopes. Our level of on-site presence depends on project needs—some projects require more direct involvement than others, but we’re always available when needed.
10. Do you provide BIM modeling or clash detection?
BIM modeling and clash detection are handled by our Virtual Design and Construction (VDC) team, a key part of our Building Performance Solutions group. Our MEP team works closely with VDC to identify critical MEP considerations—like routing limitations, code-required clearances and system coordination—to ensure potential conflicts are caught early and the client’s priorities are reflected in the final model.