Preventing Maintenance Woes through Smart Design
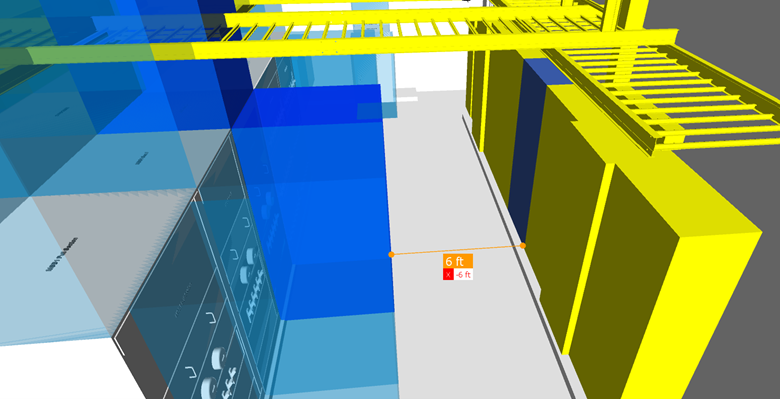
In the fast-paced world of manufacturing design and construction, the importance of incorporating thoughtful design early in the project cannot be overstated. A well-planned design phase is not just about aesthetics or initial functionality; it is crucial for ensuring long-term maintainability and operational efficiency. By proactively addressing potential maintenance challenges—such as avoiding the placement of critical equipment behind obstructive columns or ensuring machinery is not positioned over essential drainage systems—project teams can prevent costly disruptions and inefficiencies down the line. Early design considerations enable a smoother, more manageable operational phase, ultimately safeguarding the project’s success.
KEY CONSIDERATIONS FOR SMART DESIGN
Design Priorities That Drive Success
When designing process and packaging equipment systems for food and beverage manufacturing facilities, here are five of the most important topics to consider early in the project lifecycle:
1) Safety & Ergonomics: Design all equipment layouts with safety in mind, including features like emergency stop buttons, guards, and proper labeling. Invite maintenance representatives to participate in key design reviews, and, as a best practice, require all Original Equipment Manufacturers (OEMs) to complete and provide a copy of their completed machine guarding risk assessment with maintenance tasks specified. Furthermore, consider the ergonomics of maintenance tasks to reduce the risk of injury and improve efficiency. This includes designing equipment at appropriate heights and providing machine specific tools that reduce strain on workers.
2) Layout: The layout of equipment in manufacturing facilities is crucial for operational efficiency and safety. Poorly planned equipment arrangements, such as placing machinery too close together or not allowing adequate clearance for doors or maintenance, can cause installation delays, increase downtime, and create safety risks. For example, if a piece of equipment can’t be accessed due to spatial constraints, repairs and maintenance become difficult. A well-designed layout ensures smooth workflows, easy access for technicians, and safer working conditions, ultimately boosting productivity. It’s essential to plan equipment placement with enough room for maintenance, cleaning, and repairs.
3) Preventive Maintenance: Require all OEMs to provide a preventive maintenance schedule with recommendations to regularly check and replace wear components, lubricate machinery, and perform other essential tasks. This helps prevent unexpected breakdowns and extends the lifespan of equipment. Just like how regular oil changes or tune-ups keep your car running smoothly, preventive maintenance for your line equipment can help avoid unexpected breakdowns.
4) Automation & Monitoring: Implement automation and monitoring systems to track equipment performance and predict maintenance needs. This can help identify issues before they become major problems and reduce downtime. Incorporate maintenance standards, such as programming logic and hardware preferences, into the RFPs sent to all OEMs and design partners.
5) Spare Parts Inventory: Require all OEMs to provide a detailed spare parts list with critical spares called out, supplier specific part numbers that can be found online, itemized pricing, and lead times identified. Prior to the equipment shipment, ensure that the inventory of critical spare parts is ordered to ensure quick replacements and minimize downtime. This includes having a system in place to track parts’ usage and reorder as necessary.
6) Training & Documentation: Include a training budget, as required, for all OEM equipment and integrators. Ensure that each company provides comprehensive training for maintenance staff and operators. Ensure that detailed documentation and manuals are available for all equipment to facilitate proper maintenance and troubleshooting.
By focusing on these topics, you can build trust with the maintenance team early in the project lifecycle and enhance the reliability and efficiency of your food and beverage manufacturing operations for years to come.
FOUNDATIONS OF SUCCESS:
KEY CONSIDERATIONS FOR SMART DESIGN
Addressing this list upfront leads to fewer costly maintenance issues down the line. There are many factors to consider—safety, layout, preventable maintenance, automation, training and more. Navigating this process can be difficult, but investing time and resources upfront will pay off in the long run.