Using private public partnerships for infrastructure projects
In collaboration with Bart Jacobson, PMP, CEM, LEED AP, General Manager, Siemens
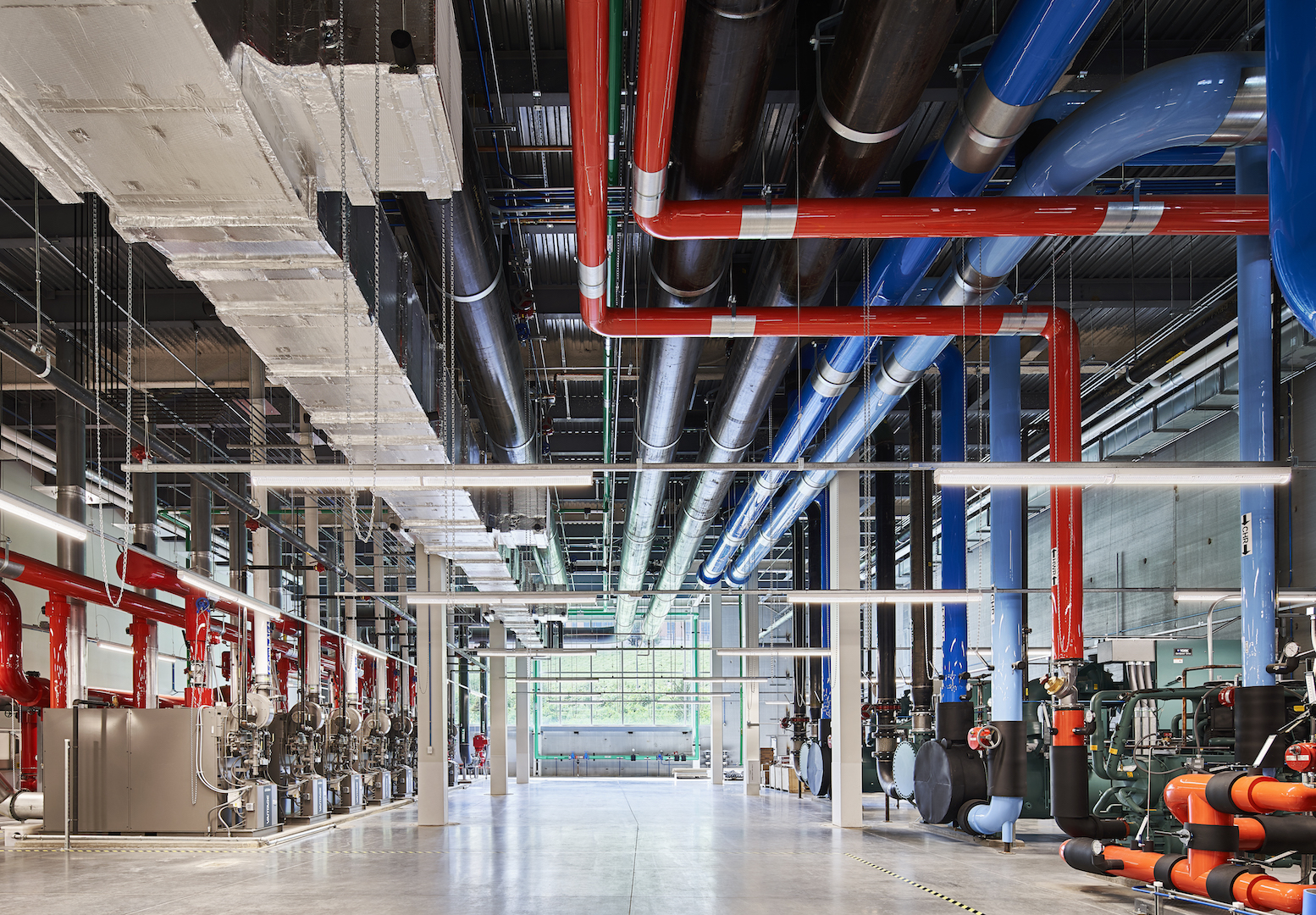
Looking for ways to fund energy infrastructure projects on campus? The public private partnership (P3) financing model can complement design-build projects to provide value and efficiencies to higher education campuses.
Why choose a P3?
P3 leverages the strongest skillsets of each public and private partner to achieve a better and faster outcome than could be accomplished alone. The P3 model can be productive for each party. Private entities can reap the benefits of a steady revenue stream while accepting the project risk and private entities can save their limited capital for other strategic needs. P3’s purpose is to design, construct, operate, maintain, and in some situations, own the infrastructure so that it can operate efficiently. The higher education market has a tremendous opportunity for the P3 model.
Public private partnerships are unique for infrastructure construction.
P3s are about using the capital of a private firm and blending the expertise of public and private entities to build, operate and maintain public projects. Common examples are higher education laboratory buildings or municipality parking garages funded by private companies with expertise in the construction and operation of these buildings.
P3 can be particularly effective when the need exists for long-term visioning, cohesive design between multiple buildings served, and costlier technologies to be effective and efficient for the long term. The P3 model can be a great fit for new energy infrastructure construction or much needed energy infrastructure upgrades because it redirects the responsibility of finding an energy generation and/or distribution solution, ensuring proper and consistent maintenance routines and operational continuity, and securing the capital away from the public sector to the private sector.
A Symbiotic Partnership
Not all building owners have the capacity to operate and maintain a facility to maximize cost and energy-saving potential. Lack of skilled labor and budget cuts can hinder public companies’ ability to maintain and operate critical infrastructure. Private firms fill that need by assuming the ownership and operational risk of capital renewal with Energy as a Service (EaaS). They use their capital to facilitate the construction or expansion of the energy infrastructure such as a central utility plant (CUP) and maintain/operate the CUP using expert building knowledge, leveraging of advanced technologies, experience and in some cases, staff.
Using a P3 approach, the CUP upgrades can happen at once to achieve operational and utility savings today instead of incurring high and unpredictable future costs if it was performed traditionally piecemealed over multiple years with deferred maintenance funds.
Consider the construction of a solar array on a building rooftop. The private firm owns, constructs, and maintains the asset, being the solar array itself. The building owner grants the private firm permission to occupy its rooftop in exchange for the right to purchase the power produced by the solar array at an agreed-upon fixed rate for a long-term time period, typically 20-25 years. The private firm forecasts electricity production and assumes performance risk for the duration of the contract.
Benefits and drawbacks of using a P3 for infrastructure
Benefits and drawbacks of utilizing a P3 method will vary from customer to customer, and project to project. Individual owner requirements will determine if P3 is the best method for achieving infrastructure goals.
A major benefit is the speed in which projects can be completed.
The availability of capital allows much needed replacements or renovations to happen at one time while allowing the user to benefit from higher efficiency equipment without having to pay entirely upfront. The alternate scenario would require the public entity to perform the deferred maintenance/replacements in small pieces over a larger period of time which could negate any energy savings achieved. The piecemeal method can also result in higher “per project” costs as efficiencies realized through material procurement and labor economies of scale cannot be achieved.
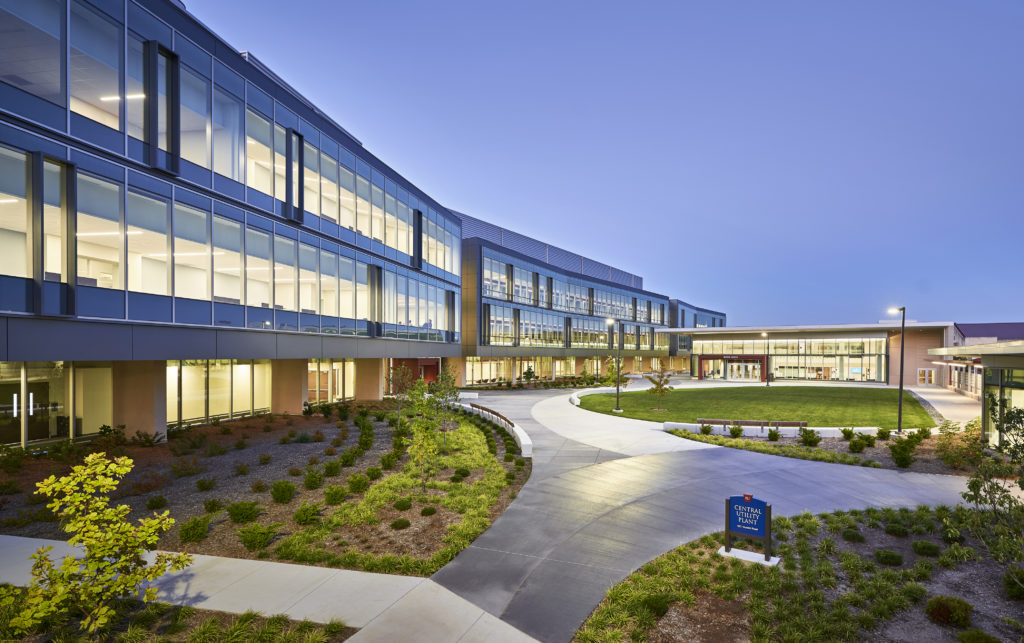
Secondary benefits of using a P3 model can result in a more cohesive vision and coordinated effort and available public budgets can be redirected to more strategic needs of the private entity.
A potential drawback to P3 can be the extra time needed by involving more than one party. While this can be seen as a drawback, the collaboration and cross-examination of each partner’s ideas and approach prevents defaulting to the status quo. This allows for projects to be designed to meet public customer lifecycle priorities, leveraging new technologies and reaching their highest potential.
Case Study: Siemens and Southern Methodist University
Siemens is the comprehensive energy partner to Southern Methodist University (SMU) and has responsibilities across strategic energy planning, energy supply and risk management, building automation and energy efficiency, campus utilities, operations and maintenance, and sustainability programming. SMU’s Energy Manager is a Siemens employee, reporting into SMU’s Office of Facilities Planning and Management. SMU’s main campus in Dallas, TX includes over 80 buildings and 6.3 million square feet.
Specific and on-going Siemens activities at SMU include:
- Upgrades to building automation and controls, access control, security, video surveillance, and fire protection. Integrated control platform for these disparate services.
- Campus-wide modernization of energy infrastructure including buildings and central plant (includes replacing chillers, boilers, cooling towers, and controls)
- Implementation of fault detection and diagnostics across SMU’s 80 campus buildings and integration into campus work order management system. With support from remote Siemens Digital Services Center and on-site services, cloud-based analytics are processed and drive a campus-wide continuous commissioning program.
- Energy conservation measures include building and lab controls, energy management system, Demand FlowTM chiller optimization, retro-commissioning, lighting controls, LED retrofits, lab controls upgrades (10 buildings), and mechanical control sequences optimization.
- Campus-wide operations and maintenance, including central utility plants.
- Energy supply management program including natural gas and electricity procurement and hedging.
A primary objective at SMU is to modernize campus-wide building automation to include remote performance monitoring and diagnostic analytics toward reducing on-going maintenance costs by leveraging technology and transitioning SMU from a reactive to a planned and predictive maintenance program. Consistent with the P3 model, Siemens owns performance commitments and risk related to reducing SMU’s energy use, cost and on-going campus maintenance requirements.
“To take us to where we wanted to go, we needed someone who would share our vision and our sincere ambition toward real modernization. At SMU, we are laying the foundation for the campus of the future…. Siemens has helped us develop our vision and acted as a trusted partner and advisor, leveraging their local expertise and global resources.” – SMU’s Chris Regis, Vice President Business and Finance